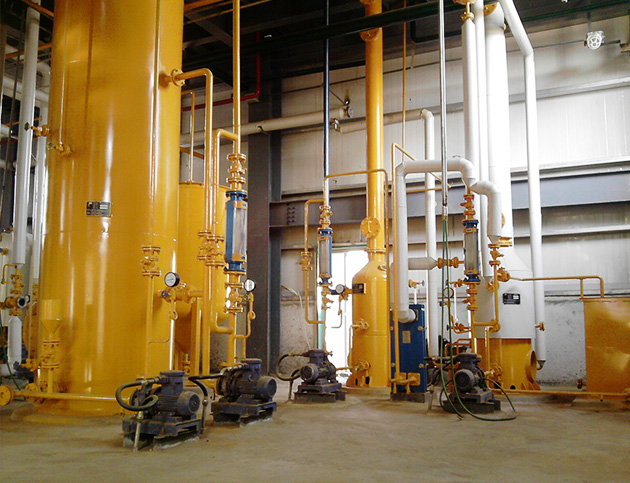
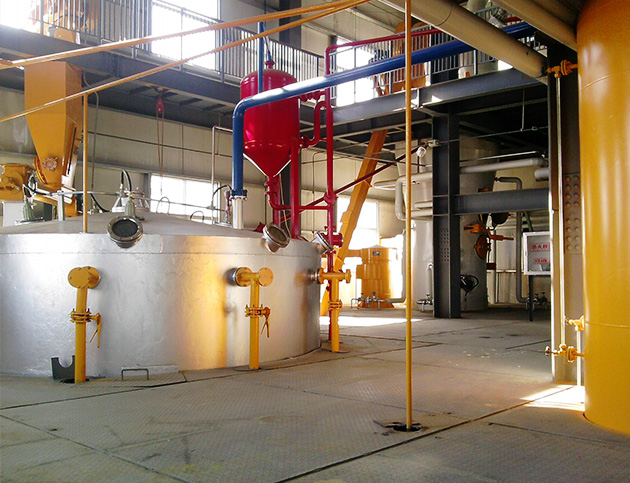
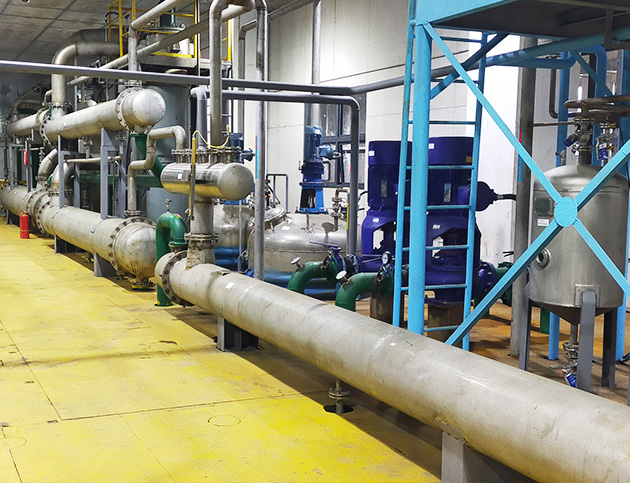
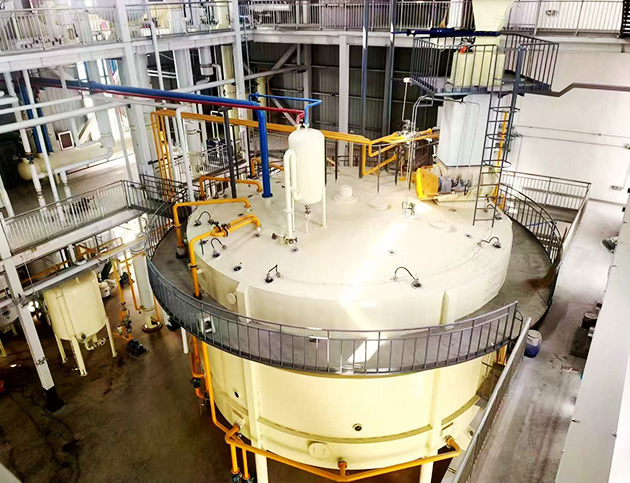
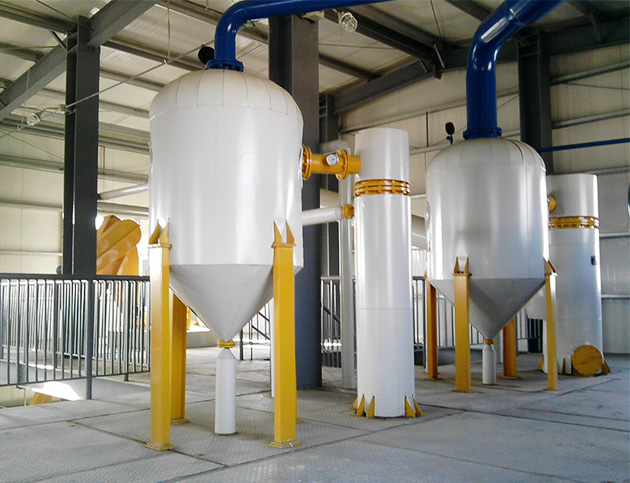
Leaching machinery
The oils eed embryo (or pre-pressed cake) immersed in selected solvents, so that the oil dissolved in the solvent (composed of mixed oil), and then mixed oil and solid residue (meal) separation, mixed oil and then according to the different boiling points for evaporation, vapor extraction, so that the solvent vaporization into steam and oil separation, so as to obtain oil (leaching crude oil).
Description
1.Process Flow
Solvent Solvent condensation recycling recycling
Material embryo→leach →Wet meal desolvation→meal→drying →cooling→Refined meal
oil mixture→vaporization→steam stripping →Crude oil filtration→Leaching out the oil→refining
Solvent condensation recycling recycling
The oils eed embryo (or pre-pressed cake) immersed in selected solvents, so that the oil dissolved in the solvent (composed of mixed oil), and then mixed oil and solid residue (meal) separation, mixed oil and then according to the different boiling points for evaporation, vapor extraction, so that the solvent vaporization into steam and oil separation, so as to obtain oil (leaching crude oil). Solvent vapor is condensed, cooled and recycled for further use. The meal also contains a certain amount of solvent, which is dried after dedissolving and drying treatment. The solvent vapor emitted during the dedissolving and drying process is still condensed, cooling and recycled.
2.Intermittent Leaching
2.1 Intermittent operation
Intermittent leaching is performed in a closed container, after each processing a certain amount of oil, stop operation, discharge and clean, and then start the next batch.
2.2 High flexibility
Intermittent leaching is more suitable for processing different kinds of oils, and the process parameters can be flexibly adjusted to suit different raw materials.
2.3 Suitable for small-batch production
Intermittent leaching is more suitable for small-scale or experimental production requirements.
2.4 Simple operation
Compared with continuous leaching, intermittent leaching equipment is relatively simple and has low maintenance cost.
2.5 Relatively low solvent recovery efficiency
Since cleaning is required after each treatment, solvent recovery and reuse are not as efficient as continuous leaching.
2.6 Application scenarios
• Small plant or pilot line.
• Process small batches of multiple oils.
• Need to change ingredient types frequently.
3.Continuous Leaching
3.1 Continuous operation
Continuous leaching is completed in a continuous process, where oil and solvents continuously enter the system, and products (meal and crude oil) are continuously exported.
3.2 High degree of automation
Continuous leaching process usually adopts automated control system, which can realize stable production process and reduce the influence of human factors on production.
3.3 high efficiency
Due to continuous operation, the production efficiency is relatively high and suitable for large-scale industrialized production.
3.4 High solvent utilization
The continuous leaching process minimizes production costs by maximizing solvent recovery and reuse through an efficient solvent recovery system.
3.5 Stable product quality
Due to the constant process parameters, and we have a more consistent product quality.
3.6 application scenarios
• Large-scale industrial production.
• The occasion with higher production efficiency requirement.
• Production lines requiring long-term and stable operation.
4.Wet meal transpiration process
4.1 Pre-desolution
After the wet meal leaves the leachers, it is first subjected to an initial desolventization process. This process is usually carried out in a closed vessel to minimize solvent evaporation.
4.2 Evaporative desolubility
After the pre-desolventization process, the wet meal is fed into the evaporator. In this process, the wet meal is heated under reduced pressure to rapidly evaporate the solvent.
In order to improve the evaporation efficiency, the evaporator is usually designed with multi-stage evaporation chambers to gradually reduce the solvent content in the meal.
4.3 Condensation recovery
The evaporated solvent vapors are fed into a condenser where they are cooled to a liquid state for recovery and reuse.
The condensed solvent can be returned to the leaching process for further use, reducing solvent consumption.
4.4 Meal drying
After the desolventization process, the meal still contains a certain amount of moisture and requires further drying. The drying process is also usually carried out under reduced pressure to prevent the nutrients in the meal from being destroyed.
The drying equipment may be a fluidized bed dryer or other types of drying equipment to ensure uniform drying of the meal.
4.5 Cooling and storage
Finally, the dried meal is cooled to a suitable temperature and then packaged or stored directly.
Cooling prevents the meal from heating up and deteriorating during storage.
5.Mixed oil treatment process
5.1 Pretreatment (preliminary separation)
Evaporation: The leached oil mixture is fed into an evaporator and heated under reduced pressure to evaporate the solvent (e.g. hexane) from the oil. This process initially separates most of the solvent.
Flash vaporization: Sometimes evaporation is followed by flash evaporation to further accelerate solvent separation.
5.2 Solvent Recovery
Condensation: The evaporated solvent vapors are cooled to a liquid state through a condenser for recycling.
Purify: Recovered solvents need to be purified to remove impurities and ensure that their quality meets the criteria for reuse.
5.3 Crude oil treatment
Filter: After initial separation the crude oil usually needs to be filtered to remove larger impurities.
Refine: The refining process consists of the following sub-steps: degumming, deacidizing, decolorizing, deodorizing, dewaxing (if applicable), and, for some oils, such as peanut oil, removal of the waxy components by freeze crystallization and filtration to improve oil clarity.
5.4 Refined oil
Cooling and storage: After refining, the oil needs to be cooled to a suitable temperature and then packaged or stored directly.
pack: Refined oil products are filled according to the market demand for easy sale.
6. Solvent recovery tools
6.1 Primary separation
Filtration or centrifugation: The leached mixture (mixture of meal and solvent) is first initially separated by methods such as filtration or centrifugation to remove most of the solid meal. This reduces solvent carry-over losses during subsequent evaporation.
6.2 Evaporative desolventization
Evaporator: After the initial separation, the liquid (a mixture containing solvent and a small amount of residue) enters the evaporator, where it is heated under reduced pressure to evaporate the solvent. Evaporators are typically designed as multi-stage evaporators to gradually reduce the solvent content.
Vacuum evaporation: To lower the boiling point of the solvent, reduce energy consumption, and prevent oils from deteriorating due to high temperatures, evaporation is usually carried out under reduced pressure conditions.
6.3 Condensate recovery
Condenser: The evaporated solvent vapors are cooled through a condenser to a liquid state for recycling. The condenser is designed to ensure that the vapors are efficiently converted to the liquid state.
Condensate treatment: The condensate produced during the condensation process needs to be treated to avoid pollution of the environment.
6.4 Solvent purification
• Deodorization: Recovered solvents need to be deodorized to remove possible odors.
• Filtration and purification: Remove impurities in the solvent by filtration and other purification means to ensure that its quality meets the standards for reuse.
6.5 Solvent storage
Storage tanks: Purified solvents are stored in special containers for reuse. The storage tanks should be well sealed to prevent evaporation of the solvent.
Technical Parameters
Application Field
Related Products
Inquiry
Please Feel to give your inquiry in the form.We will reply you in 24 hours.