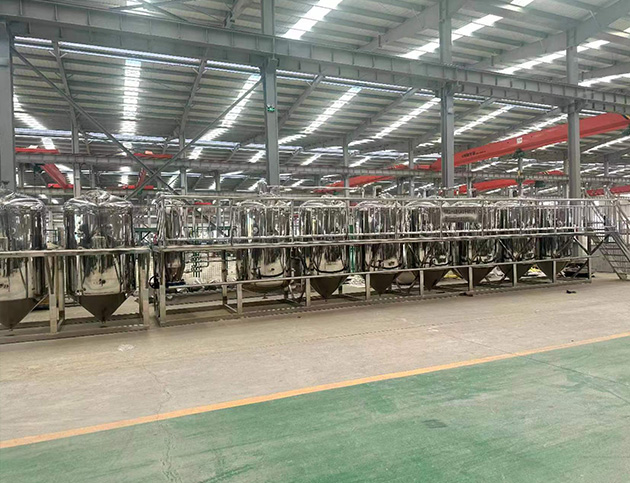
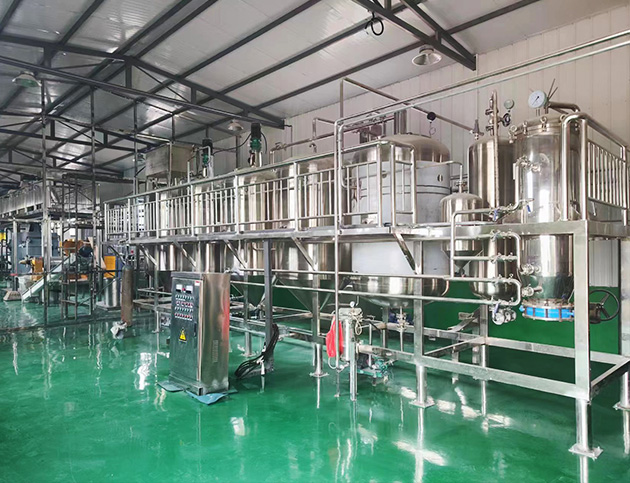
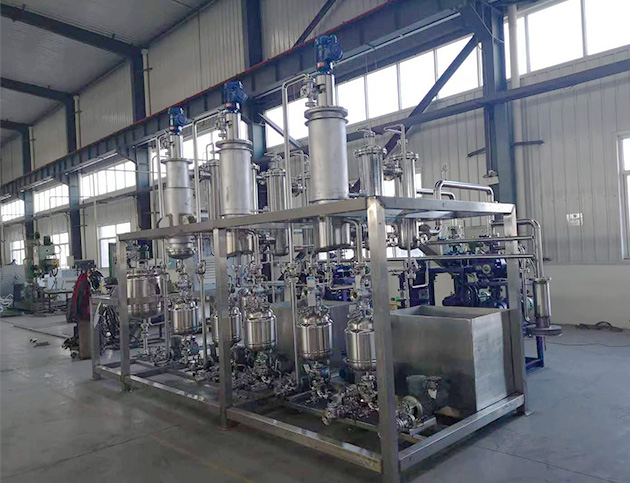
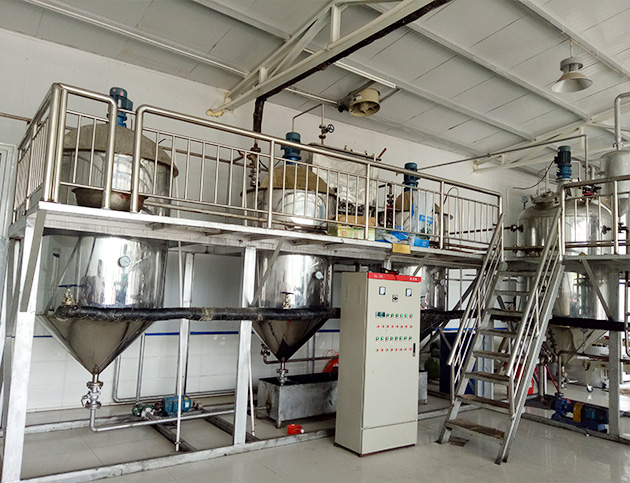
Refining production line
- Deacidification, degumming, decolorization, deodorization project
- Dewaxing and degreasing engineering
Description
Deacidification, degumming, decolorization, deodorization project
1.Process flow
2.Specific Operation
2.1 Filtering
Crude oil ((or coarse filter crude oil)) pumped into the refining pot (general gross oil mechanical impurities ≤ 0.2%) loading oil for the refining pot of about 75%.
2.2 Alkali cooking
① Before alkali refining, first make preparations for alkali refining oil refining, the hot water tank and lye tank according to the previously determined acidity, impurities, color of the gross oil, alkali refining, the concentration of hot brine and lye needed to be prepared for use. (Generally, the concentration of brine is 0.7~1%, and the temperature is 65℃~80℃, which is 5~10℃ higher than the final temperature of oil, or the same temperature. The concentration of lye is 12~22 Be°, low Be° for low acid value, high Be° for high, depending on the quality of the crude oil).
② Open the refining pot slow stirring (about 30 rpm / min), slow stirring for 10~20 minutes, can remove most of the oil foam, and then in conjunction with the role of stirring, open the heating medium valve to the oil heating, when the oil temperature rises to 40~60 ℃, this time for the initial temperature of the oil. Close the heating valve of the oil, close the slow stirring, open the fast stirring (60 ~ 70 rpm), while opening the lye box lye valve, the pre-matched and calculated quantitative lye in 5 ~ 10 minutes, add to the crude oil for neutralization, the general neutralization time of 10 ~ 40 minutes, while in the meantime, we should constantly use a stainless steel spoon or plate to take the oil that is being neutralized to be observed. If small particles are found, open the heating medium valve to warm up the oil, the oil warming rate of 0.5-1 ℃ / min, the final temperature of the oil is higher than the initial temperature of the oil 10 ℃ as well as the closing of the heating medium valve. To be seen in the refining pot of soap floc, grease can be in the spoon can quickly precipitate to the bottom, close the stirrer, let the pot of alkali refining oil static precipitation 5 ~ 8 hours, precipitation time to time, open the pot under the side of the release of the soap foot valve, put the net of all the soap foot, close this valve, the alkali oil into washing pot or wash in the pot.
2.3 Rinsing
Alkali refined oil in the water washing pot, with slow stirring to raise the temperature, the final temperature rises to 80 ℃, close the heating valve, open the pre-prepared hot brine on the oil for water washing (water time is generally mastered between 5 ~ 10% minutes, the water added is generally 8~10% of the oil weight), after adding the water, close the water-filling valve, and at the same time turn off the stirrer, so that the oil in a stationary state of precipitation for 1.5 ~ 2 hours, Open the lower water release (put soap foot) valve,remove all the water and residual soap, that is, the completion of the first washing, general washing for 2 ~ 3 times, repeat the above washing operation steps and parameters can be completed 2 ~ 3 times washing. Washing standards: the waste water clean, less foam, no precipitation impurities, Phenolphthalein titration showed a neutral, washing oil to do the high temperature test of 280 ℃ without precipitation, that is, for the qualified washing oil.
2.4 Dehydration
Close all the valves on the decolorizing pot connected with the decolorizing pot, only open the vacuum valve on the pot, open the vacuum pump to pull the negative pressure, when the vacuum gauge on the pot shows more than -0.6Mpa vacuum, then open the oil inlet valve connected with the water washing pot to pull all the water washing oil from the dehydrating pot to the decolorizing pot, and then turn on the decolorizing pot when all the oil is entering the decolorizing pot, close the oil inlet valve connected with the dehydrating pot and open the decolorizing pot to stir, open the heating valve of the decolorizing pot to the oil, and make the oil temperature rise to 100~120℃ with the stirring.Stir the decolorizing pot, open the heating valve of the decolorizing pot to the oil, and make the temperature of the oil rise to 100~120℃ under the condition of stirring.Maintained at this temperature for about 30 minutes, the negative pressure is maintained above -0.8Mpa, and observed through the sight glass, the oil surface bubbles are few, no water droplets on the sight glass, can be regarded as dewatering qualified, the theoretical requirements of the need to decolorize the oil water content can not be >0.1~0.15%, otherwise affect the decolorization effect.
2.5 Decorating
After the dehydration is completed, the oil temperature in 100 ~ 120 ℃, close the oil heating valve, with mixing will be quantitative decolorant in the negative pressure is not less than -0.85Mpa state as soon as possible will be added to the decolorant in the oil, bleaching and decolorization of the oil, decolorant and the oil in the high-temperature contact time is generally about 20 minutes (or 30 minutes), and then turn off the vacuum pump, open the vacuum valve to break the vacuum, so that the degree of vacuum down to 0Mpa, decolorization section can be completed, the general amount of decolorant added to the oil weight of 2 ~ 6% (according to the bleaching soil), decolorant bleaching soil, activated carbon, etc., the domestic general use of these two kinds of the main, can be used individually, can be used in combination.If the ratio of general activated carbon and bleach soil is 0.3:1,0.5:1,1:1, etc. Because of the expensive price of activated carbon, the general manufacturers use very little, but the effect is better than that of bleaching soil in all aspects.Please manufacturer refer to use.
2.6 Filtering
a: Filtration
The decolorized oil will be stirred (at this time, the decolorized pot is at atmospheric pressure), open the inlet valve of the filter and the outlet valve of the decolorized pot and the outlet valve of the oil filter, turn on the decolorized pump and pump the decolorized oil in the decolorized pot with the stirring, and the oil to be filtered will be pumped into the filter, and the oil will be separated from the decolorizer until the oil to be filtered is filtered out, then close the stirring of decolorizing pot, decolorizing pump, oil outlet valve of decolorizing pot and oil inlet valve of filtering machine, meanwhile open the air inlet valve of air compressor and filtering machine, and press the air into the filtering machine, and then close the valve of oil outlet when no oil can be seen in the oil outlet tube, and the filtering section will be finished.
b:Oil pressure
While closing the oil outlet valve, open the oil outlet valve under the filter, press the oil in the filter back to the decolorizing pot, close the oil outlet valve under the filter when the oil flow is not visible from the oil return pipe, and end the oil pressure section.
c:Blow-drying
After the end of the oil pressure section, close the oil outlet valve under the filter at the same time, open the dirty oil outlet valve, the filter cake in all the residual oil blowing out, blow-drying time is 20-30min, close the air inlet valve and air compressor. Then open the filter emptying valve, empty the filter pressure, open the filter below the waste soil outlet valve, while opening the vibrator, unloading waste soil, blow-drying section end. Plate and frame filter working pressure is generally ≤ 0.35Mpa, such as over the cake can be unloaded (decolorant) after loading and then work. Blade filter general working pressure ≤ 0.4Mpa.
2.7 Deodorization
Check and close all the valves connected with the deodorization pot, open the vacuum valve of pumping deodorization, open the vacuum pump, when the vacuum degree in the deodorization pot reaches ≧0.6Mpa or above, open the entry valve of the deodorized oil to be deodorized, and suck the deodorized oil to be deodorized into the deodorization pot under vacuum, then close the entry valve of the deodorized oil to be deodorized, and open the deodorization pot to be deodorized when the oil heating valve heats the deodorized oil.When the oil temperature rises to 105 ~ 110 ℃, and then slowly raise the direct steam valve, to be deodorized oil began to steam deodorization,
When the oil temperature rises to 220℃ -240℃, in a high vacuum, high temperature, with 2-3 kg of pressure direct steam vaporization, maintain 2 ~ 4 hours can be, and then turn off the direct steam, Continue to work for about 0.5 hours under high temperature and high vacuum, depending on the pan of the oil surface is calm, no vapor overflow, you can turn off the oil heating valve, in the maintenance of high negative pressure (high vacuum), open the deodorization pot on the water cooling valve on the oil, began to cool the oil in the pot.When the oil in the pan is cooled to below 80℃, close the water cooling valve, vacuum pump, open the broken vacuum valve, break the vacuum, so that the pressure in the pot is 0Mpa, you can open the bottom of the pot of the oil valve and the output pump, will be deodorized oil pumped into the finished product tanks,the refining section is finished.
Be°---- denotes: Mei Shi Baume degree (abbreviated Baume degree). The concentration of liquid alkali can be determined by the Baume degree and hydrometer.
Naoh---- means: sodium hydroxide.
Comparison table of sodium hydroxide content and specific gravity of lye of different
Baume degree(15℃)
波美度(Be。) | Naoh 含量(%) | 比重 |
12 | 8.140 | 1.09 |
13 | 8.97 | 1.1 |
14 | 9.7 | 1.11 |
16 | 11.1 | 1.125 |
18 | 12.8 | 1.14 |
20 | 14.6 | 1.165 |
22 | 16.14 | 1.18 |
24 | 17.6 |
1.20 |
The "Specific Gravity" item is mainly used to convert the weight of caustic soda into volume.
Dewaxing and degreasing engineering
Oil winterization dewaxing and degreasing project is an important oil refining process, the main purpose of which is to remove wax and high melting point triglycerides from oils and fats, and to improve the transparency, low temperature stability and taste of oils.
1.Process flow
2.Operation steps
2.1 Pre-boot preparation
Before starting the machine, first check the running condition of each equipment, whether it is running normally, to prevent turning over, whether the screws at the connection are loose, whether the speed reducer is refueled, whether the link valve is leaking oil, whether the speed reducer, the water pump, the oil pump, the air compressor, the refrigeration unit has any abnormal sound, vibration, and the various inspections are not different before starting the machine.
2.2 Boot-up operation
The deodorized oil in the deodorization pot cooled to 70 degrees, open the crystallization tank oil inlet valve, open the deodorized oil storage tank oil pump, transfer the oil into the crystallization tank, close the oil pump and oil inlet valve when the oil level rises to 90% of the crystallization tank height, and at the same time open the crystallization tank stirring device (10-13r/min) and the water valve, the water on the oil to slowly cool to 40 degrees at a cooling rate of 1-2 ° C / h cooling rate, maintain 4-5 hours later, open the freezer to drop 1-1.5 degrees per hour rate, the oil temperature cooling 32 ℃ to stop cooling, maintain the temperature into the crystal 4-5 hours, after observing to be crystal grain growth solid,opening the crystal tank outlet valve and the screw pump.Put the crystal oil into the winterization filtration machine filtration, the pressure is not greater than 0.4Mpa, the solid fat retained within the filter, the liquid from the outlet into the finished oil tank.After filtering, close the screw oil pump and oil outlet valve, open the filter plate of winterization filter, unload the solid fat, and complete the operation of winterization fractionation.
2.3 Technical advantages
● Improvement of oil quality
Winterization dewaxing and degreasing works for oils can remove waxes and high melting point triglycerides from oils, making the oils clearer and more transparent, with better low-temperature stability and better taste.
● Increase the added value of products
After winterization dewaxing, degreasing treatment of oil, the quality is higher, suitable for high-end food, cosmetics and other fields, increasing the added value of the product.
● Energy saving and environmental protection
The project adopts physical methods such as cooling crystallization and filtration separation, which does not require the use of chemical reagents and reduces the pollution to the environment. At the same time, through reasonable process design and equipment selection, energy saving and consumption reduction can be realized.
Technical Parameters
Application Field
Related Products
Inquiry
Please Feel to give your inquiry in the form.We will reply you in 24 hours.